Monoblock Cooling Units
Production of Refrigeration and Freezing Monoblocks
In cooling and freezing monoblocks, we use the ecological refrigerant – propane R290, which provides high energy efficiency and safety in operation. This responds to global ecological standards and increasingly stringent norms regarding GWP and ODP indicators.
Due to the growing needs of the refrigeration market, Moody Group – Moody Refrigeration continuously perfects the production processes of monoblocks and designs further Plug&Play solutions. It’s worth adding that the Moody Group – Moody Refrigeration monoblock production line is located in Turkey.
The monoblock is an advanced Plug&Play solution that is a complete device ensuring the maintenance of the appropriate temperature in cooled spaces in chambers, tables, showcases, and other refrigeration and freezing devices. Depending on the model, low-temperature monoblocks are designed to operate at temperatures ranging from -10°C to +15°C. Freezer monoblocks, e.g., for freezer chambers, are intended for a temperature range from -25°C to -15°C.
Every production process of cooling or freezing monoblocks begins from the design phase, where engineers use CAD software to design a device intended for a specific refrigeration furniture. Moody Group – Moody Refrigeration designers advise at every stage, which eliminates potential problems at an early stage of the project. The R&D department conducts a series of tests, measurements, and performance analyses. It’s important for the device to be not only functional but also energy-efficient and safe to use.
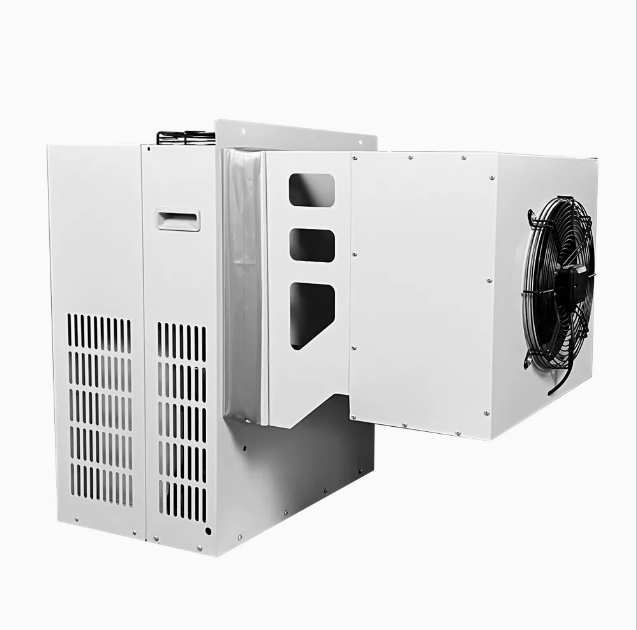
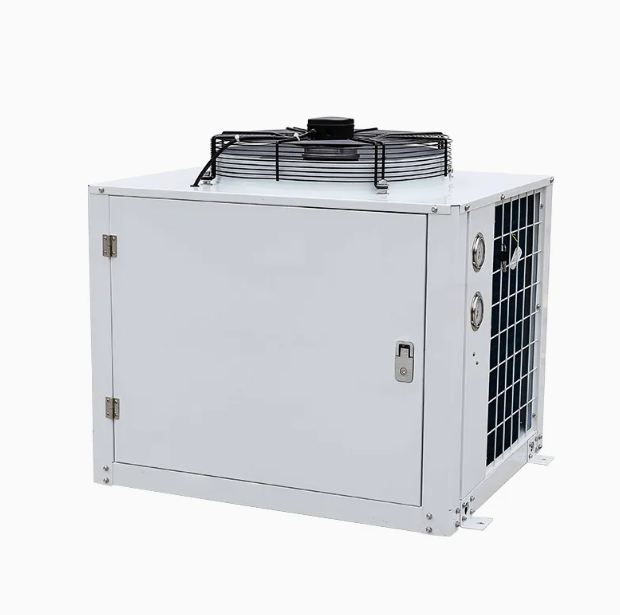
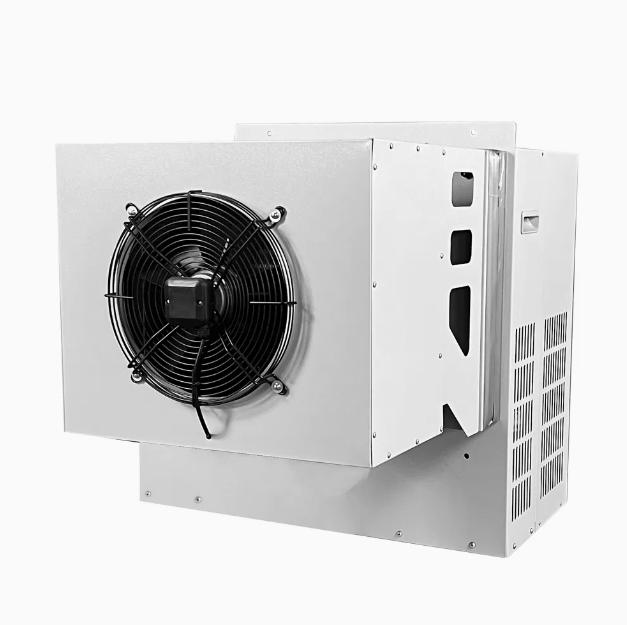
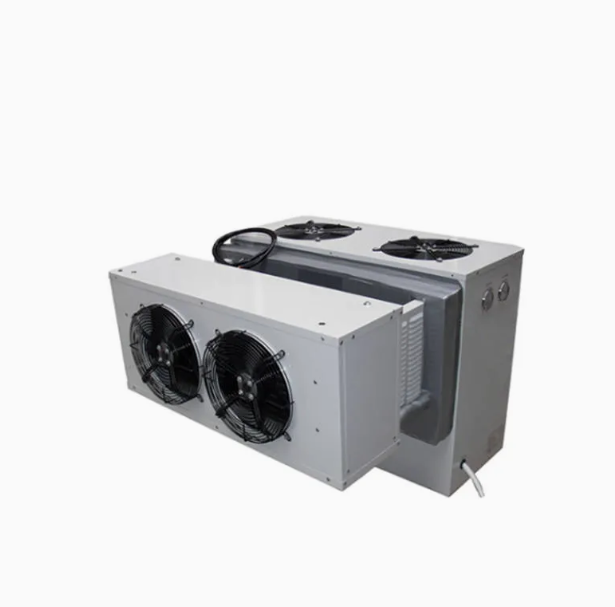
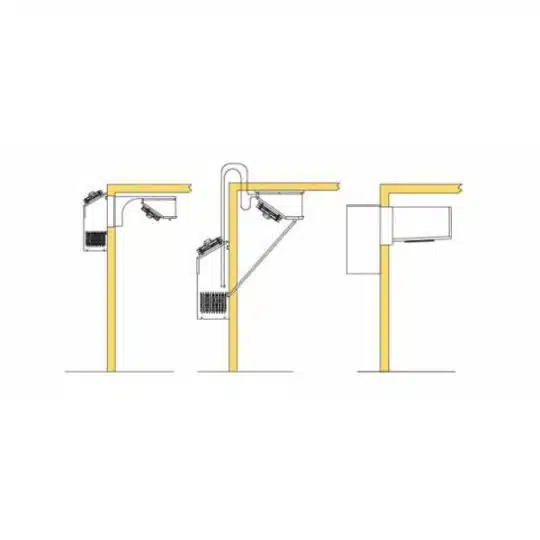
Our technological lines, equipped with modern machines and devices, allow for the serial production of monoblocks, ensuring high quality. Each stage of production is closely monitored, ensuring execution excellence in line with the highest standards. Delivery punctuality for our direct recipients is significant.
A key element in the production of monoblocks is the selection of appropriate components
and high precision during assembly. We use the highest class components:
Secop, Embraco, or Cubigel compressors,
Copper tubes prepared by our CNC machines,
Energy-efficient EBM, EC Fans & Drives motors,
CAREL, Dixell controllers.
This translates into long service life and reliability of monoblocks. The assembly process requires particular accuracy, so each element is carefully assembled, and the finished monoblocks are subjected to rigorous control tests.
One of the main advantages of monoblocks is their easy and quick installation. Depending on the device, the installation of a monoblock can take only a few minutes. An example of a place with quick installation is refrigeration tables, where the exchange is simple and can be performed by a person trained to carry out this operation, without specialized refrigeration training.
Tunel Group integrates cutting-edge technology into their Cold Room Monoblock Units, ensuring superior performance and reliability:
Advanced Control Systems: Equipped with digital control panels, thermostats, and sensors for precise temperature management.
PLC/SCADA Integration: Enables real-time monitoring and automated control, enhancing operational efficiency and ease of management.
Energy-Efficient Compressors: Utilize state-of-the-art compressors that deliver powerful cooling while minimizing energy usage.
High-Quality Coils: Designed with staggered copper pipes and aluminum fins, ensuring efficient heat exchange and durability against corrosion.
Electronic Expansion Valve with Fuzzy Control: Ensures high refrigeration efficiency and fast cooling speed.
Optional Defrost Systems: Available with E1 or E2 defrost systems to prevent ice buildup, maintaining consistent performance and reducing maintenance needs.
Hot Gas Defrosting on Demand: High efficiency and energy saving, completing defrosting within 3 to 5 minutes and saving more than 80% energy compared to electrical heaters.
Smart Automation: Intelligent control systems manage
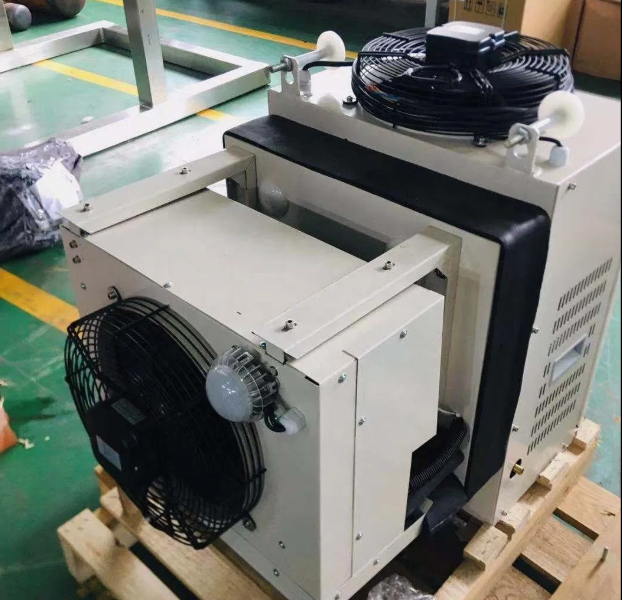
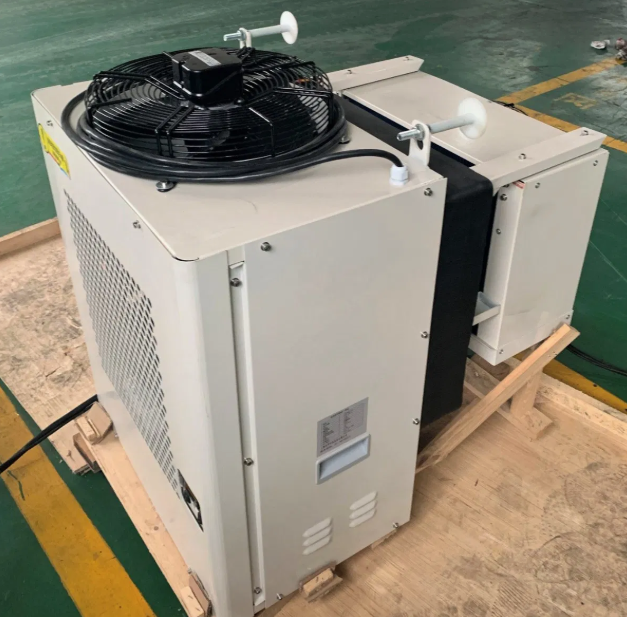
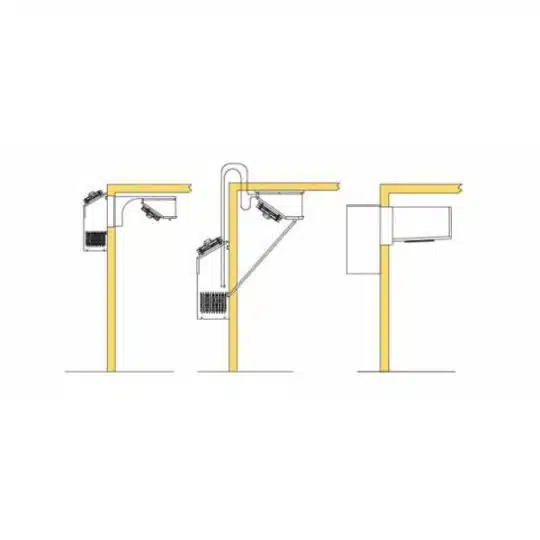